
Much has been heard and said about the semiconductor shortage in the automotive industry in the post-pandemic world over the past two years. Semiconductors are used in vehicles for safety systems through to powertrain and infotainment systems.
According to some estimates, an average car today has between 1,400 and 1,500 chips. The New York Times counted as many as 3,000 chips used in a modern-day vehicle.
Today, it is almost cliché to say that cars are computers on wheels – a quote attributed to various tech and automaker c-suite members.
The total automotive semiconductor market was estimated at roughly $38bn in 2020 by Allied Market Research. It is expected to grow to $114bn by the end of 2030, implying a compound annual growth of 11.8%. This is relatively small part of the overall global semiconductors market, estimated by the Semiconductor Industry Association to stand at around $574bn.
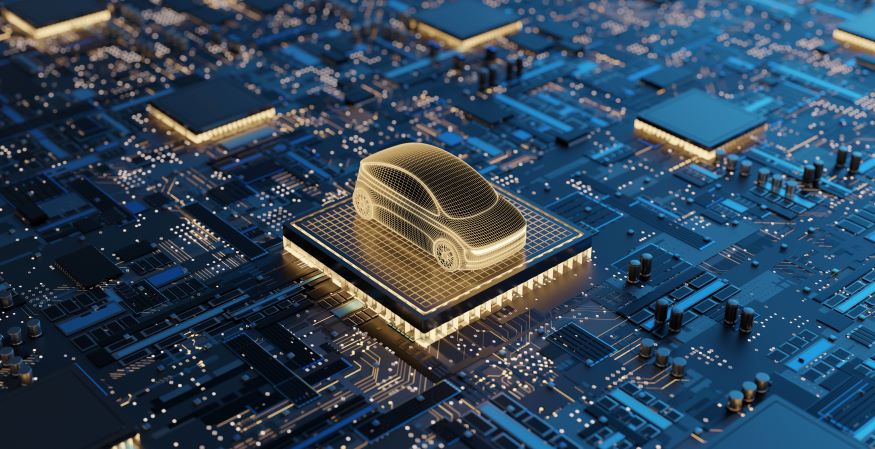
The main driving force behind this expected growth has to do with a chip shortage but also with deeper trends in the automotive sector. The industry has been on the path to electrification for some time now, with the rise of electric and hybrid vehicles.
According to data by the EV-Volumes.com, a database on global EV sales, by the end of 2022, the market share of EVs (including battery electric and plug-in hybrids) accounted for 13% of the total of all vehicles sold. As recently as 2016, that share was less than 1% of the total and just north of 4% in 2020.
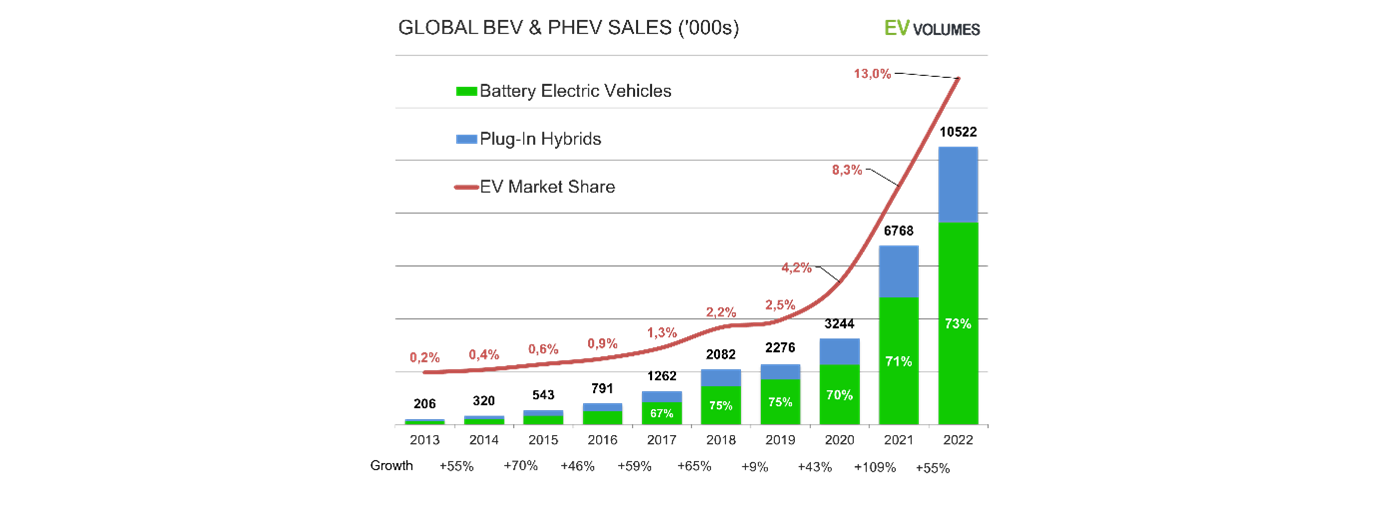
This shift in the automotive sector has deep implications for semiconductors. According to a Deloitte analysis, electric vehicles require more and better electronic components than traditional internal combustion engine vehicles.
The same is true for autonomous vehicles. While it is not certain when vehicles may reach L4 or L5 full autonomy, many sensors and electronic components will be needed along the way. The more sophisticated the computational power and data storage required, the higher the number of control and storage chips required will be.
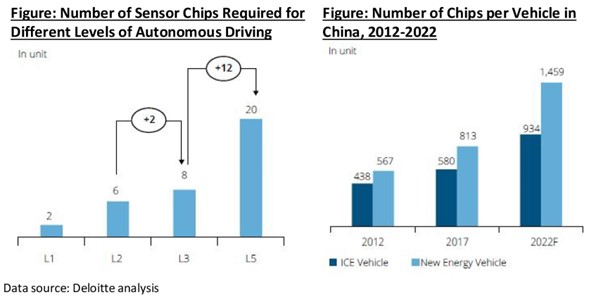
According to the Deloitte analysis, the number of more sophisticated sensor chips increases drastically with higher levels of driving autonomy. Similarly, the estimated number of chips in non-internal combustion engine vehicles was considerably higher than in internal combustion engine vehicles in China.
The pandemic-induced chip shortage
Recently, automakers got into trouble with the much-reported chip shortage. The covid-19 pandemic caused disruptions in global supply chains. On the one hand, logistics and transportation hurdles such as port closures affected the global availability of both finished semiconductors as well as the rare raw materials used for their manufacture. These raw materials include germanium, silicon and gallium arsenide, which are extracted and processed mostly in China.
The war in Ukraine has exacerbated the problem because the country used to supply nearly half of the world´s purified neon gas, essential for semiconductor manufacturing. Russia supplies between 25% and 30% of palladium globally, a rare metal used for semiconductors. Palladium is used in the metal connections attaching chips to circuit boards and in the junctions between the chips and other metals.
The semiconductor shortage affects all industries using semiconductors but there was another issue specific to automotives, highlighted by a McKinsey piece. Most OEMs and suppliers use a “just in time” manufacturing strategy. This means they drastically decreased their orders of chips when the covid-19 pandemic broke out in 2020, leaving them low on inventory when demand subsequently recovered.
This led to the demand for semiconductor chips increasing rapidly after covid-19 lockdowns. McKinsey estimates the automotive industry ordered a 10% to 20% surplus of semiconductors above what it needed to ensure sufficient inventory. This is likely the reason that some CEOs from the chip industry such as Pat Gelsinger, of Intel, expected the shortage to extend into 2024.
According to S&P Global, the global shutdown impacted heavily semiconductor manufacturing companies across the globe, stopping wafer production. “Once a fab is online, it takes 26 weeks to fill the production pipeline from wafer start to completion. Wafers are processed in lots or batches that take 12 weeks to cycle through the fab (14 to 20 weeks for complex process technologies). An additional 12 to 14 weeks are required for testing, die bonding and packaging. Manufacturers prioritised the existing semiconductor inventory to fill orders, so as fabs came back online, production was already lagging demand.”
According to a Deloitte analysis, automotive grade semiconductor chips generally need to be more durable and reliable than those found in other electronics. However, automotive-graded semiconductor production is limited and manufacturers’ willingness to expand capacity for the production line is relatively weak.
All of this has had a deep impact on the automotive industry in the past couple years. The chip shortage was estimated to translate into $210bn of revenue losses in 2021 for the automotive sector globally, according to consulting firm AlixPartners, cited by CNBC. More recently, in its latest earnings call, Ford blamed a shortfall of 100,000 vehicles during the fourth quarter of 2022, mostly on the chip shortage.
Chip-laden vehicles
While it is true that integrated circuit components installed in the car body are generally not as demanding, it is other electronic components in a modern-day vehicle that must be able to continue to operate in “harsher” environments. These components must remain operational in a much wider range of temperatures, which may vary from -40°C to +155°C, according to Market Prospects.
One of the most important elements in automotive electronics is the electronic control unit, which acts like a computer in charge of major systems in a vehicle. As the complexity of modern-day vehicles increases, the number of electronic control units increase as well. According to data cited by Market Prospects, there are hundreds of electronic control units in premium vehicles of BMW and Benz today.
More image sensors are deployed inside and outside a vehicle today than ever before in a push for improved safety. Advances in driver assistance technology, autonomy and related imaging technologies all require high-tech sensors.
VC deals in automotive semiconductors
Despite their important role in automotive electronics, VC-backed deals in pure-play automotive semiconductors are uncommon, according to PitchBook data. There were spikes in such deals in 2021 and 2022, as the chip shortage worsened. The median deal size and post-money valuation of automotive semiconductors also rose in 2021 and 2022 compared with previous years.
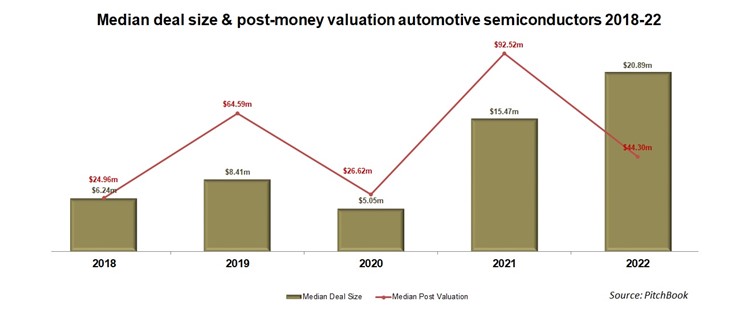
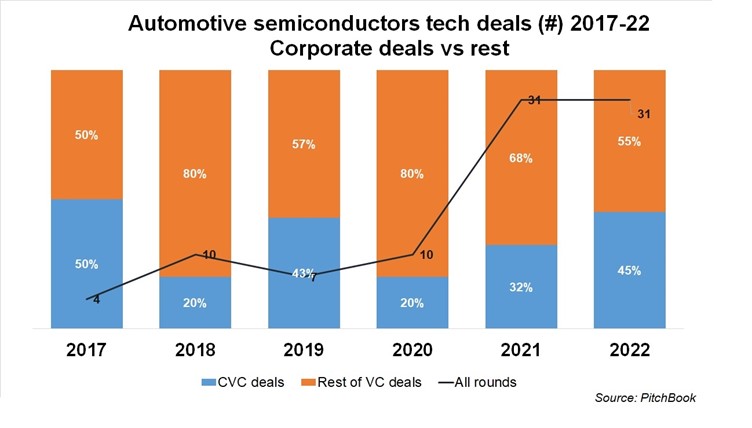
Semiconductor businesses – like most other hardware businesses – do not tend to get as much attention in the VC sector because of their high failure rates. The majority of these deals, according to PitchBook, were in early and seed stage rounds.
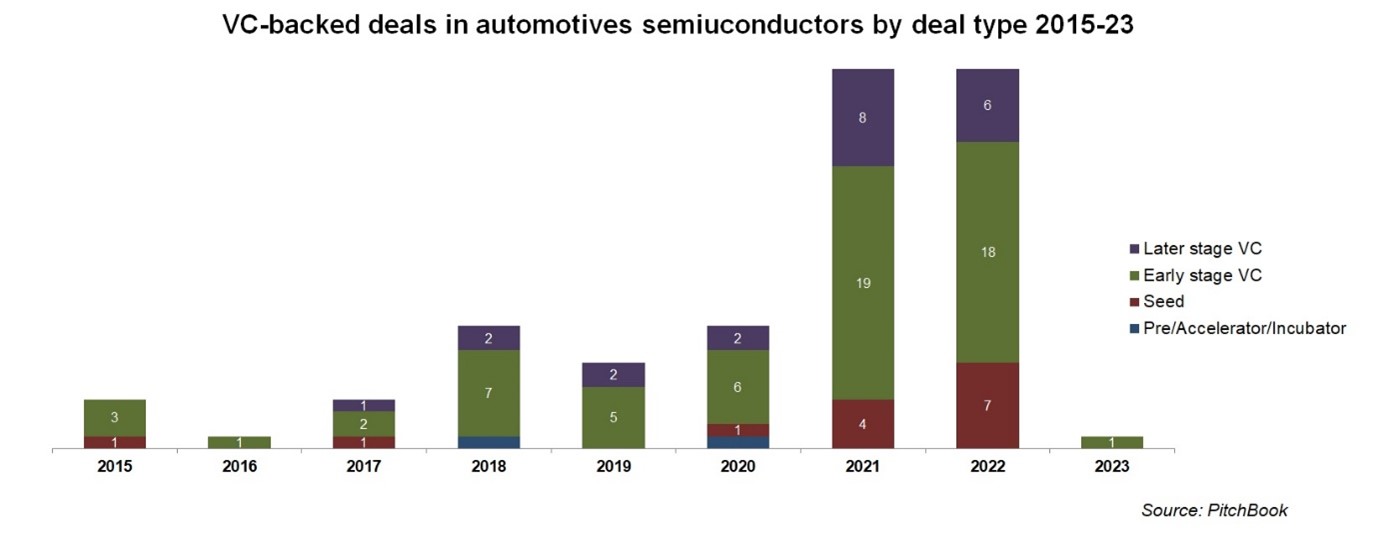
Most of those VC-backed deals have taken place in Asia, which has been, for quite some time, a manufacturing powerhouse. Despite deglobalisation trends, the region is likely to retain its dominance.
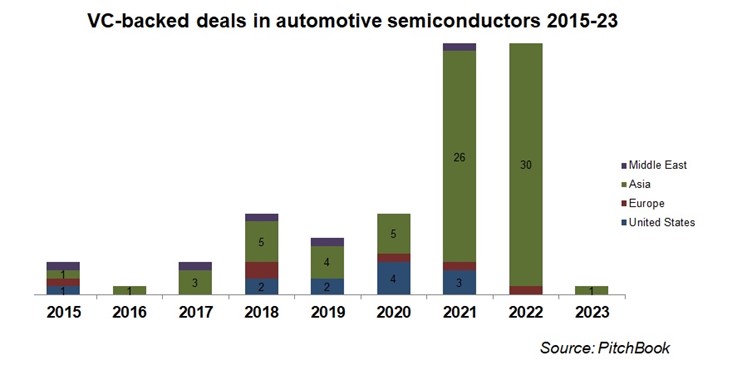
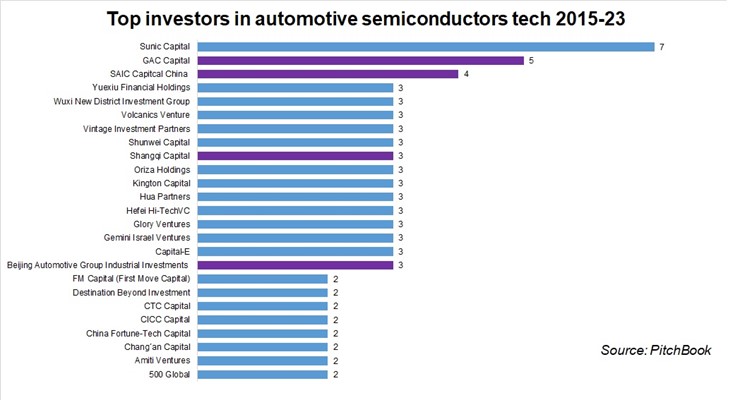
However quickly or slowly the chip shortage gets resolved, the longer-term sustained demand for semiconductors is likely to stay, even in a recession. Electrification of transport is the biggest growth driver for chips and is unlikely to stop as the world moves towards carbon neutrality and net zero.