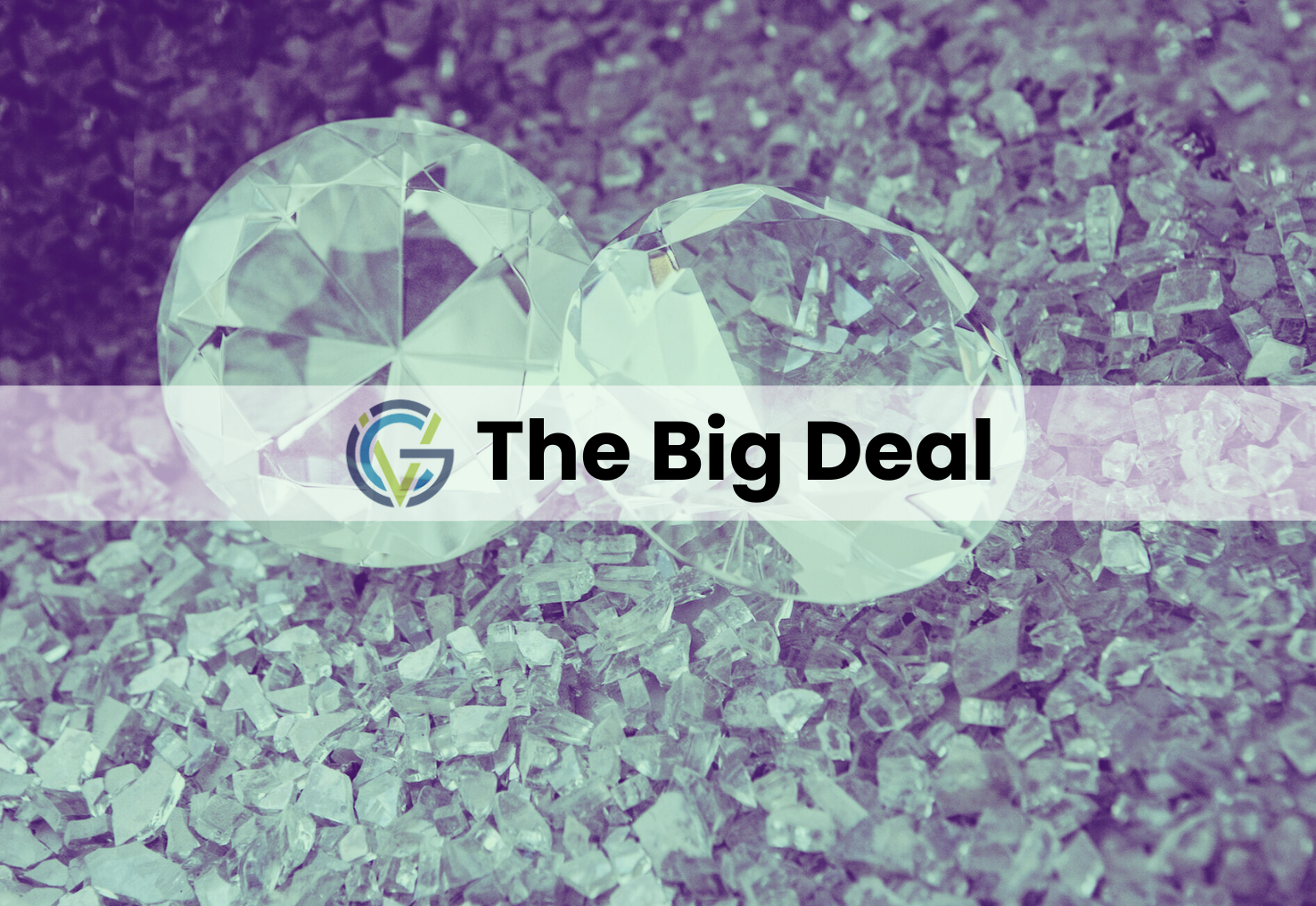
How can you tag and verify objects in the supply chain to weed out counterfeits, verify things haven’t been contaminated and keep critical components safe? Tracking is a huge problem in managing supply chains, and no one quite knows the best way to solve it.
But Dust Identity may have a solution — give everything a unique fingerprint by sprinkling it with diamond dust.
The Massachusetts-based company, which just raised $40m in a corporate-backed series B round, has developed a system that uses engineered diamond dust to create one-of-a-kind markers on each object that it claims are clone-proof. Each one is married to a digital identity that can have data added to it over time.
Think of it the way you would a person, says co-founder and CEO Ophir Gaathon. There is a vast array of data on a person from their birth certificate to their medical records and educational qualifications, and it doesn’t matter that they’re in different places because the person at the centre still has a unique identity.
“We basically mapped the same technical approach for parts,” he adds. “We’re creating an identity management system for physical objects that allows us to authenticate them using tools that are very similar to biometrics. But because there’s no ‘bio’ in mass-produced objects, we had to create a unique identifier.
“We use a little bit of diamond dust, sprinkle it on the object – it can come in a polymer, it can be spray-coated, painted, it can be part of a part – and the footprint is so small it can fit on tiny components and small objects. From that point, we basically have a fingerprint we can authenticate, and once we do that you can almost think of it as a credit card transaction.”
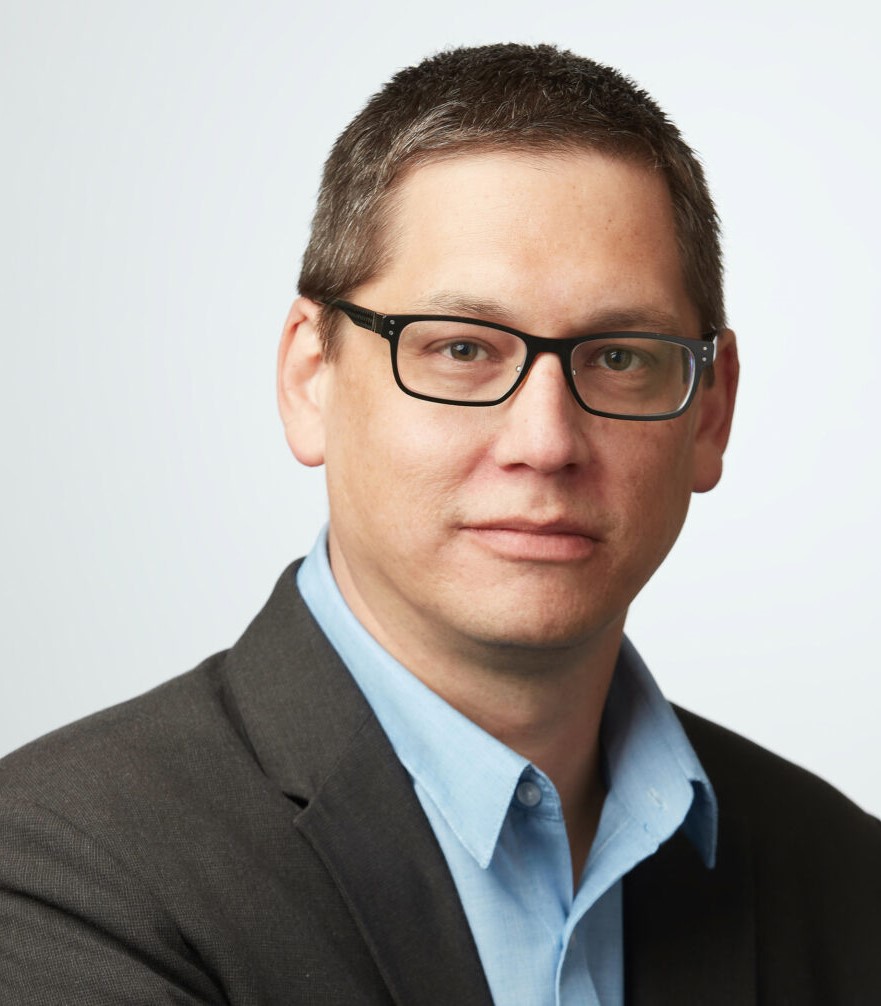
Gaathon (left) and fellow co-founders Jonathan Hodges and Dirk Englund originally met while conducting university research on using diamonds in cooling or sensing for quantum computing, and so they have a good idea of the material.
You might think it would be an expensive material but Dust’s diamonds aren’t jewellery grade. They’re taken from the parts too small to be used in the abrasives industry, which makes the cost “neglible” according to Gaathon, and the company has built its technology around their physical properties.
“We have methods where we can see the diamonds and their orientation,” Gaathon says. “We have a way to create an extremely complex fingerprint using every individual crystal on an object that makes it impossible for anybody to clone or replicate.
“Diamond is chemically inert on one side, so it doesn’t have the toxicity issues of some materials that can be carcinogenic or foreign. But it also has an extraordinarily high level of durability. If you want to have a tag that survives for the full lifetime of an object and which can store the value we want to, there are not a lot of other materials out there.”
The technology attracted aerospace manufacturer Airbus and payment services firm American Express, both of which took part in the series B round through their venture units. Gaathon describes them – along with existing backer Lockheed Martin – as category kings, and is enthusiastic about what they bring outside of cash.
“They understand their clients, they understand the ecosystem, the supply chain,” he says. “For example, Amex’s relationship with retail, with brands and their understanding of how to craft and build better products for their card members, is something it would take us years to learn ourselves.”
Dust announced the round alongside a partnership with esports organisation Oxygen Esports, part of a bid to expand its customer base from hardware manufacturers to consumer products like luxury goods, art and memorabilia. It’s an area where authenticity becomes more important the more expensive the piece is, but while Dust’s solution might be more durable and less cloneable, the company is looking beyond just reducing risk.
“Putting diamonds on things is not where we think the value is, it’s the consumption of information from the data around that fingerprint”
“Putting diamonds on things is not where we think the value is, it’s the consumption of information from the data around that fingerprint,” Gaathon says. Take artificial intelligence, which has been hot for the last year and which could be used for a wide array of tasks in the industrial sector.
“You need a dataset that you can train your AI models on,” he says. “But the problem we have today is the data quality is not high. It’s not available, it’s not structured, it doesn’t have the level of confidence that will allow you to quantify the risk in the analysis you do around those models.”
Take Airbus and Lockheed Martin, both aerospace companies. That is not an industry that produces millions of items at the same time – manufacturing batches are usually below 10,000, Gaathon says – and that means you don’t have a statistically significant amount of data to create something resilient from an AI perspective.
“But if I can [use Dust’s technology to] pair a particular part so I know exactly the environmental conditions it went through, I now have a dataset that may be smaller but which is a lot more accurate,” he says. “And I can create better insights. That is not something you can do with QR codes, or something you can do if you’re concentrating on limiting counterfeits in the ecosystem.
“The risk-based approach is really limited. What we want to do is build that trust, create that ecosystem along with the data infrastructure that will allow the customers and stakeholders to benefit from better data quality which is available, audible and accurate.”